LEAN Automation กำจัด 7 ความสูญเสีย เพิ่มประสิทธิภาพการผลิต
การนำระบบอัตโนมัติ (Automation) เข้ามาใช้ในโรงงานเพื่อเพิ่มผลผลิตและลดต้นทุนเป็นทั้งเป้าหมายสำคัญและความท้าทายที่ผู้บริหารโรงงานต่างมุ่งหวัง โดยเฉพาะผู้ที่ต้องการให้โรงงานพัฒนาไปสู่การเป็น Smart Factory เพื่อรองรับความต้องการในตลาดที่เติบโตขึ้นเรื่อยๆ แต่การเปลี่ยนโรงงานให้กลายเป็นโรงงานอัจฉริยะ ไม่ใช่เพียงแค่การลงทุนในเครื่องจักรราคาแพงหรือหุ่นยนต์ล้ำสมัยเท่านั้น สิ่งที่สำคัญยิ่งกว่าคือการเตรียมหน้างานให้พร้อมก่อนการปรับใช้ให้เข้ากับระบบอัตโนมัติ ซึ่ง Lean Automation เป็นกุญแจหลัก วันนี้ Solwer จะอธิบายให้ฟังว่า Lean Automation คืออะไร แล้วมันมีประโยชน์อย่างไรต่ออุตสาหรกรรมยุค 4.0 นี้กัน
Lean Automation คืออะไร?
You May Also Like
Lean Automation หรือ ระบบอัตโนมัติแบบลีน คือการผสานหลักการลีนเข้ากับระบบอัตโนมัติ โดยมุ่งเน้นที่การปรับปรุงกระบวนการผลิตเพื่อเพิ่มคุณค่าให้ลูกค้า ไม่ใช่แค่การเพิ่มประสิทธิภาพของแต่ละขั้นตอน แต่ยังพิจารณาถึงประโยชน์ที่ลูกค้าได้รับจากผลิตภัณฑ์ ในขณะที่พยายามลดต้นทุนให้มากที่สุด
เมื่อพูดถึงการทำงานแบบอัตโนมัติ หลายคนอาจคิดว่าการลงทุนในระบบอัตโนมัติจะเพิ่มค่าใช้จ่าย ซึ่งขัดแย้งกับหลักการของลีนที่เน้นการลดต้นทุน อย่างไรก็ตาม ต้นทุนที่ลีนพยายามลดไม่ได้หมายถึงเพียงแค่เรื่องของเงินเท่านั้น และการนำระบบอัตโนมัติมาใช้ไม่จำเป็นต้องลงทุนในอุปกรณ์ราคาแพงเสมอไป แต่เป็นการออกแบบกระบวนการที่คุ้มค่าและมีประสิทธิภาพสูงสุด
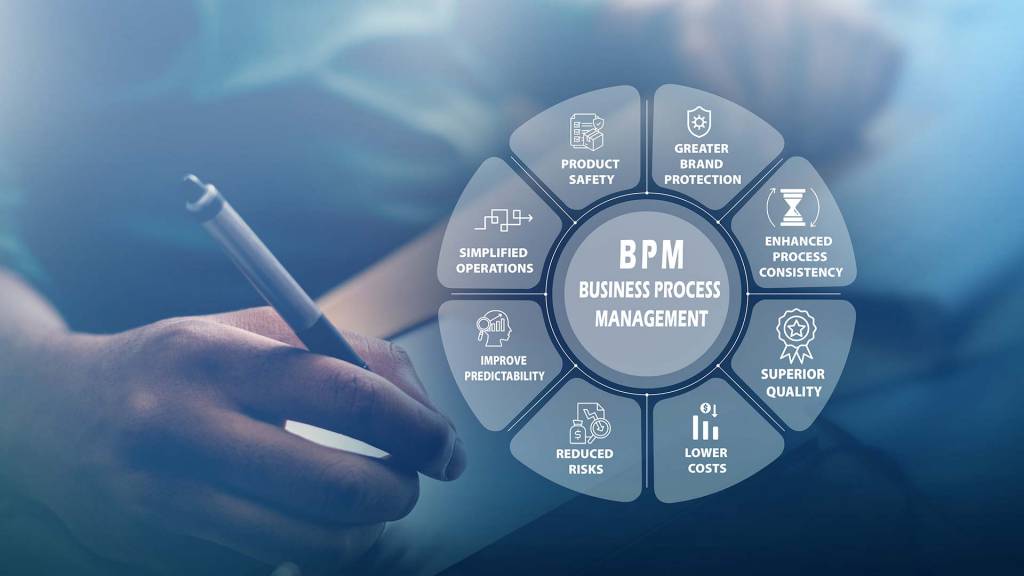
หลักการของ Lean Automation
1. การคิดเชิงระบบ (Systems Thinking)
- มุ่งเน้นการปรับปรุงคุณค่าที่ลูกค้าได้รับจากผลิตภัณฑ์ในภาพรวม
- ไม่ใช่แค่การเพิ่มประสิทธิภาพของแต่ละกระบวนการเท่านั้น
2. การลดความสูญเสีย (Waste Reduction)
- ใช้เทคโนโลยีอัตโนมัติช่วยลดความสูญเสียในด้านต่างๆ เช่น ความผิดพลาด, การรอคอย, การเคลื่อนไหวที่ไม่จำเป็น
- เน้นการออกแบบกระบวนการที่กำจัดความสูญเสียอย่างเป็นระบบ
3. การลงทุนอย่างพอดี (Right-Sizing Investment)
- ไม่จำเป็นต้องทุ่มลงทุนในเทคโนโลยีอัตโนมัติทุกกระบวนการ
- ลงทุนเฉพาะในจุดที่จะช่วยเพิ่มคุณค่าและลดความสูญเสียได้อย่างแท้จริง
4. ความยืดหยุ่นและการตอบสนอง (Flexibility & Responsiveness)
- ออกแบบระบบอัตโนมัติให้มีความยืดหยุ่น สามารถปรับเปลี่ยนได้ตามความต้องการ
- ช่วยเพิ่มความสามารถในการตอบสนองต่อการเปลี่ยนแปลงของตลาดและความต้องการของลูกค้า
ความแตกต่างระหว่าง Traditional Automation และ Lean Automation
1. เป้าหมายการปรับใช้
- Traditional Automation: มุ่งเน้นที่การเพิ่มกำลังการผลิตโดยใช้เทคโนโลยีอัตโนมัติในการทำงานซ้ำ ๆ แทนแรงงานคนให้ได้มากที่สุด เพื่อลดข้อผิดพลาดจากมนุษย์และเพิ่มความเร็วของการผลิต แต่ยังไม่เน้นเรื่องการลดขั้นตอนที่ไม่จำเป็น
- Lean Automation: มุ่งเน้นการลดของเสียและการสร้างคุณค่าให้กับลูกค้า โดยไม่ใช่แค่เพิ่มกำลังการผลิต แต่พิจารณาถึงกระบวนการที่ให้ผลลัพธ์ที่ดีที่สุดสำหรับลูกค้า และใช้เทคโนโลยีอัตโนมัติเท่าที่จำเป็นเพื่อเพิ่มประสิทธิภาพของการทำงาน
2. วิธีการลดต้นทุน
- Traditional Automation: เน้นการลดต้นทุนระยะยาวด้วยการแทนที่แรงงานคนด้วยเครื่องจักร ทำให้สามารถผลิตได้มากขึ้นโดยใช้เวลาเท่าเดิมหรือสั้นลง ซึ่งอาจทำให้ต้นทุนสูงขึ้นในช่วงแรกจากการลงทุนอุปกรณ์
- Lean Automation: เน้นการลดต้นทุนในทุกขั้นตอน โดยการปรับปรุงกระบวนการให้มีความคุ้มค่า ใช้ทรัพยากรอย่างมีประสิทธิภาพ และเลือกลงทุนเฉพาะในส่วนที่จำเป็น โดยไม่จำเป็นต้องลงทุนสูงในเทคโนโลยีใหม่เสมอไป
3. ความยืดหยุ่นในการผลิต
- Traditional Automation: มักมุ่งใช้ระบบอัตโนมัติในรูปแบบเดิมที่ออกแบบมาเพื่องานซ้ำ ๆ หรือการผลิตแบบ Mass Production จึงมีความยืดหยุ่นในการปรับเปลี่ยนน้อย
- Lean Automation: มีความยืดหยุ่นมากกว่า เพราะจะออกแบบให้ตอบสนองกับการผลิตแบบเฉพาะเจาะจงที่หลากหลายได้ สามารถปรับเปลี่ยนได้ตามความต้องการของตลาดและลูกค้าโดยไม่ต้องหยุดการผลิต
4. การมุ่งเน้นการพัฒนากระบวนการ
- Traditional Automation: เน้นการเพิ่มผลผลิตและลดต้นทุนด้วยการทดแทนแรงงานในขั้นตอนต่าง ๆ ไม่ได้มุ่งเน้นที่การปรับปรุงกระบวนการที่ไม่จำเป็นหรือลดขั้นตอนที่ไม่ก่อให้เกิดคุณค่า
- Lean Automation: เน้นการพัฒนากระบวนการในทุกด้านโดยคำนึงถึงการลดขั้นตอนที่ไม่ก่อให้เกิดคุณค่า และเพิ่มประสิทธิภาพโดยการนำระบบอัตโนมัติมาช่วยในจุดที่จำเป็นเท่านั้น
5. การลงทุนในเทคโนโลยี
- Traditional Automation: มักใช้การลงทุนครั้งใหญ่เพื่อซื้อเครื่องจักรอัตโนมัติหรือระบบที่สามารถทำงานซ้ำ ๆ ได้
- Lean Automation: เลือกการลงทุนในเทคโนโลยีที่สอดคล้องกับกระบวนการที่ต้องการปรับปรุงจริง ๆ โดยเน้นการใช้งานที่คุ้มค่า ไม่จำเป็นต้องลงทุนมากถ้าไม่ก่อให้เกิดผลลัพธ์ที่เพิ่มมูลค่า
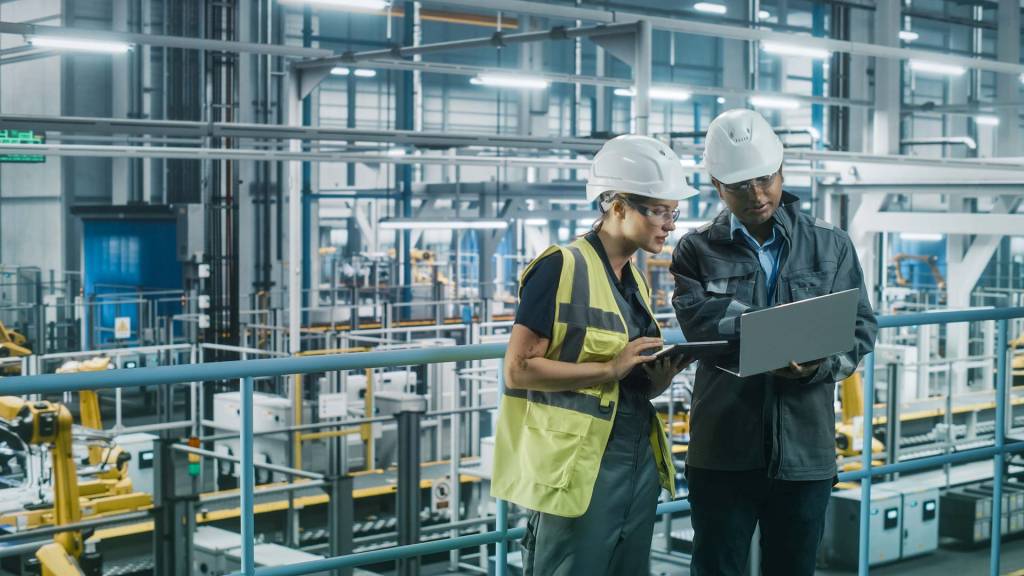
การออกแบบ Lean Automation อย่างมีประสิทธิภาพของเด็นโซ
เด็นโซให้ความสำคัญกับขั้นตอนการเตรียมพร้อมและการออกแบบระบบที่ดีเป็นอย่างมาก เพราะถือเป็นรากฐานที่สำคัญสำหรับการนำระบบอัตโนมัติมาใช้งานอย่างมีประสิทธิภาพ การออกแบบระบบโดยใช้แนวคิดแบบ Lean Automation นั้นไม่ใช่การนำหุ่นยนต์มาแทนคนเพียงอย่างเดียว แต่เราต้องคำนึงถึงการนำทักษะของคนมาใช้ในการออกแบบระบบอัตโนมัติ
ขั้นตอนแรก เราต้องกำจัด “Muda” ภาษาอังกฤษคือ “Waste” หรือ “ความสูญเปล่า” ของการทำงานของคน โดยใช้แนวคิด Lean Manufacturing ซึ่งมีการระบุถึง 7 Waste ที่สำคัญ ได้แก่ ความสูญเสียเนื่องจากการผลิตมากเกินไป (Overproduction), ความสูญเสียเนื่องจากการเก็บวัสดุคงคลัง (Inventory), ความสูญเสียเนื่องจากการขนส่ง (Transportation), ความสูญเสียเนื่องจากการเคลื่อนไหว (Motion), ความสูญเสียเนื่องจากกระบวนการผลิต (Processing), ความสูญเสียเนื่องจากการรอคอย (Delay) และความสูญเสียเนื่องจากการผลิตของเสีย (Defect) ซึ่งทั้งหมดนี้เป็นสิ่งที่ไม่จำเป็นและควรต้องตัดออกไป เพื่อให้กระบวนการทำงานมีความเพรียว เรียบง่าย และต่อเนื่อง โดยไม่ทำให้ประสิทธิภาพของงานลดลง
ตามหลักการ Lean Automation การออกแบบระบบอัตโนมัติจึงเป็นการนำเอาแนวคิดแบบ Lean มาใช้ในการพัฒนาระบบ โดยมีเป้าหมายหลักคือการลดความสูญเปล่าต่างๆ ควบคู่ไปกับการเพิ่มประสิทธิภาพการทำงาน ซึ่งสอดคล้องกับคำกล่าวของอาจารย์ Sato Kenshu ที่ว่า “กระบวนการผลิตที่ดีที่สุดคือ กระบวนการที่มีการทำงานไม่ซับซ้อนและต่อเนื่อง” การเข้าใจหลักการ Lean Automation จะช่วยให้องค์กรออกแบบและปรับปรุงระบบการทำงานได้อย่างมีประสิทธิภาพ สามารถตอบสนองความต้องการได้อย่างรวดเร็ว ลดต้นทุน และสร้างความได้เปรียบเชิงแข่งขัน
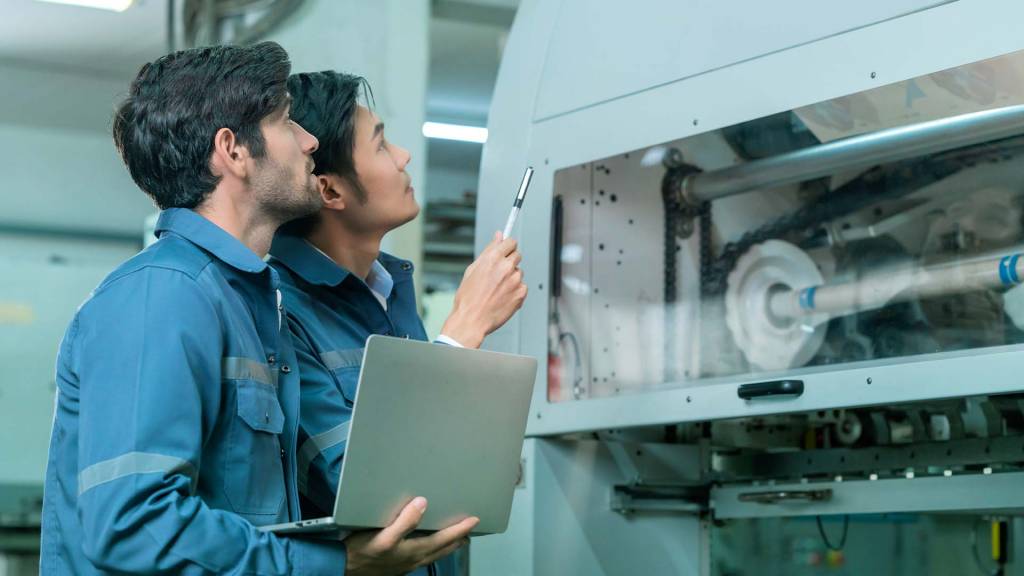
ที่มาของ Lean Automation System Integrators (LASI)
ในปี 2018 DENSO และ DENSO WAVE ได้เปิดตัวโปรแกรมฝึกอบรม Lean Automation System Integrator (LASI) ในอุตสาหกรรมที่เชื่อมต่อ (Connected Industries) เป็นส่วนหนึ่งของกิจกรรมการสนับสนุนการผลิตในประเทศไทยโปรแกรมนี้สรุปประสบการณ์และความเชี่ยวชาญในด้านอัตโนมัติมากกว่า 70 ปี ซึ่งได้รับการพัฒนาผ่านกิจกรรมการผลิต เพื่อฝึกฝนผู้รวมระบบที่มีความสามารถในการนำระบบอัตโนมัติที่มีประสิทธิภาพสูงและลีนมาใช้ในกระบวนการผลิต ในโปรแกรมนี้ การใช้ระบบอัตโนมัติไม่ได้หมายถึงแค่การแทนที่แรงงานมนุษย์ด้วยหุ่นยนต์เท่านั้น แต่ยังหมายถึงการสอนขั้นตอนของการทำให้อัตโนมัติในแบบที่มีประสิทธิภาพสูง ซึ่งรวมถึงการติดตั้งหุ่นยนต์หลังจากการปรับปรุงประสิทธิภาพของกระบวนการแล้ว โดยมีความร่วมมือใกล้ชิดกับรัฐบาลไทย มหาวิทยาลัย และสถาบันการศึกษาต่างๆ โปรแกรมนี้กำลังช่วยฝึกอบรมผู้รวมระบบในด้านหุ่นยนต์และ IoT ซึ่งเป็นทั้งสองเสาหลักของโมเดล Thailand 4.0
ขั้นตอนการนำ Lean Automation มาใช้ในโรงงาน
1. วิเคราะห์กระบวนการผลิต (Process Analysis)
- ศึกษากระบวนการผลิตทั้งหมดเพื่อระบุปัญหาที่เกิดขึ้นในปัจจุบัน เช่น ความสูญเสียในขั้นตอนต่าง ๆ การใช้เวลาหรือทรัพยากรที่ไม่คุ้มค่า
- ทำแผนที่กระบวนการ (Process Mapping) เพื่อระบุจุดที่ไม่ก่อให้เกิดคุณค่า หรือที่มีปัญหาความล่าช้า รวมถึงขั้นตอนที่สามารถปรับปรุงด้วยระบบอัตโนมัติ
2. ตั้งเป้าหมายการปรับปรุง (Define Lean Objectives)
- กำหนดเป้าหมายที่ชัดเจน เช่น ลดเวลาในการผลิต ลดต้นทุน ลดความผิดพลาดที่เกิดจากมนุษย์ หรือปรับปรุงคุณภาพของผลิตภัณฑ์
- ระบุ KPI (Key Performance Indicators) เพื่อใช้ติดตามผลลัพธ์ของการปรับใช้ Lean Automation
3. ออกแบบและปรับกระบวนการ (Process Redesign)
- รับกระบวนการให้มีความเรียบง่ายและคุ้มค่ามากขึ้น โดยลดขั้นตอนที่ไม่จำเป็น และรวมกระบวนการที่สามารถทำได้ในจุดเดียวกัน เพื่อลดการเสียเวลาและทรัพยากร
- พิจารณาการใช้เทคโนโลยีอัตโนมัติในกระบวนการที่ซ้ำซ้อนหรือต้องการความแม่นยำสูง เช่น การประกอบชิ้นงาน การบรรจุหีบห่อ หรือการตรวจสอบคุณภาพ
4. เลือกเทคโนโลยีที่เหมาะสม (Select Appropriate Automation Technology)
- เลือกเทคโนโลยีอัตโนมัติที่ตรงกับความต้องการ เช่น หุ่นยนต์แขนกล, ระบบตรวจสอบด้วยเซ็นเซอร์, ซอฟต์แวร์วิเคราะห์ข้อมูล หรือระบบ IoT (Internet of Things) เพื่อเชื่อมต่อข้อมูลและกระบวนการผลิตทั้งหมด
- เน้นการเลือกเทคโนโลยีที่คุ้มค่า ไม่จำเป็นต้องเลือกเทคโนโลยีที่มีราคาสูงเสมอไปหากไม่ตอบโจทย์ในการลดต้นทุน
5. ทดสอบและทดลองระบบ (Pilot Testing)
- ทำการทดสอบการใช้งานระบบ Lean Automation ในพื้นที่เฉพาะของโรงงาน เพื่อประเมินความเหมาะสมของการใช้งานจริง
- ตรวจสอบว่าระบบสามารถลดของเสีย เพิ่มความแม่นยำ และปรับปรุงกระบวนการได้ตามเป้าหมายที่ตั้งไว้ โดยปรับปรุงจุดที่พบปัญหาในการทดสอบ
6. ฝึกอบรมพนักงาน (Employee Training)
- จัดอบรมพนักงานให้เข้าใจการใช้งานระบบ Lean Automation และการดูแลรักษาอุปกรณ์ เพื่อให้มั่นใจว่าทุกคนสามารถใช้งานระบบได้อย่างมีประสิทธิภาพ
- สร้างความเข้าใจในหลักการลีนเพื่อให้พนักงานทุกคนมีแนวคิดในการลดของเสียและเพิ่มคุณค่าในกระบวนการผลิต
7. ติดตั้งระบบจริง (Full-scale Implementation)
- ติดตั้งระบบ Lean Automation ในทุกส่วนของกระบวนการผลิตตามแผนที่ได้ทดสอบแล้ว
- ติดตั้งเซ็นเซอร์และระบบติดตามเพื่อเก็บข้อมูลการทำงานของระบบ ช่วยให้ผู้บริหารสามารถติดตามผลลัพธ์และปรับปรุงการทำงานได้อย่างต่อเนื่อง
8. ติดตามและปรับปรุง (Monitoring and Continuous Improvement)
- ติดตามผลการทำงานของ Lean Automation โดยใช้ข้อมูลที่รวบรวมได้จากระบบ เช่น เวลาที่ใช้ในการผลิต การลดลงของความสูญเสีย และประสิทธิภาพในการทำงาน
- ปรับปรุงกระบวนการอย่างต่อเนื่องตามหลักการลีน โดยประเมินผลจาก KPI และหาแนวทางในการลดของเสียเพิ่มเติม
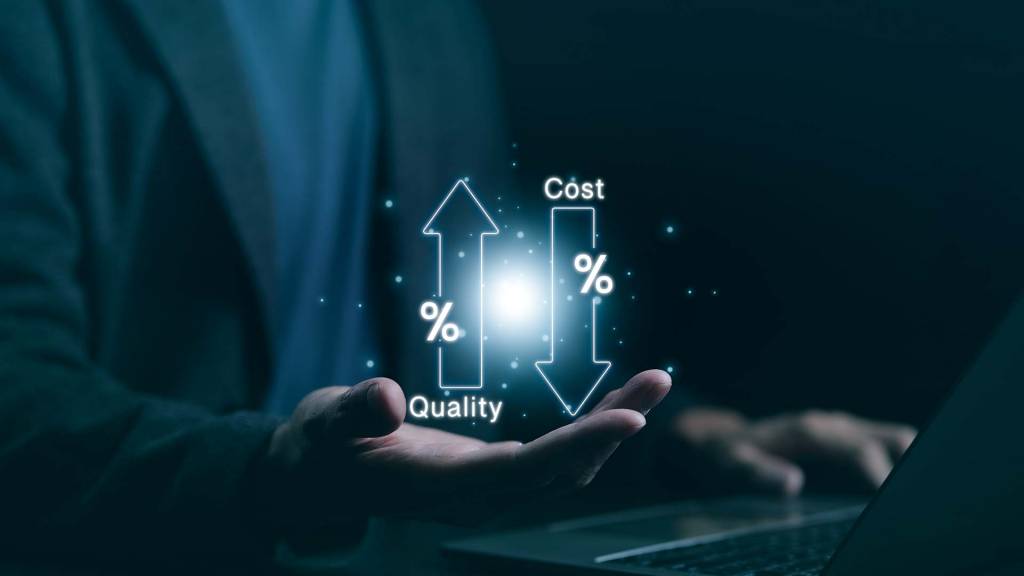
ประโยชน์ของการใช้ Lean Automation ในโรงงาน
การใช้ Lean Automation ในโรงงานหรือธุรกิจมีประโยชน์หลายประการ โดยช่วยให้กระบวนการผลิตและการจัดการทรัพยากรมีประสิทธิภาพยิ่งขึ้น ลดของเสีย และสร้างคุณค่าให้กับลูกค้าในหลายด้าน ดังนี้:
1. ลดความสูญเปล่าและของเสีย (Waste Reduction)
- Lean Automation มุ่งลดขั้นตอนที่ไม่ก่อให้เกิดคุณค่าและความสูญเสียในกระบวนการ เช่น การเคลื่อนย้ายที่ไม่จำเป็น การเก็บสินค้าคงคลังเกิน และการใช้ทรัพยากรที่ซ้ำซ้อน
- ลดความผิดพลาดในการผลิตที่อาจเกิดจากมนุษย์ ทำให้กระบวนการมีความสม่ำเสมอมากขึ้น ส่งผลให้สินค้ามีคุณภาพสูงขึ้น
2. เพิ่มประสิทธิภาพการผลิต (Increased Productivity)
- ระบบอัตโนมัติช่วยเพิ่มความเร็วในกระบวนการผลิต ทำให้สามารถผลิตสินค้าได้จำนวนมากขึ้นในเวลาที่สั้นลง
- ลดเวลารอคอยและลดระยะเวลาการทำงานในแต่ละขั้นตอน ช่วยให้กระบวนการผลิตทั้งหมดไหลลื่นและมีประสิทธิภาพสูงขึ้น
3. ลดต้นทุนการผลิต (Cost Savings)
- ลดการใช้ทรัพยากรที่ไม่จำเป็น และเพิ่มประสิทธิภาพในการใช้วัตถุดิบ ทำให้ต้นทุนการผลิตลดลง
- ลดการพึ่งพาแรงงานคนในงานที่ซ้ำซ้อน ช่วยลดต้นทุนด้านแรงงาน และช่วยให้พนักงานสามารถมุ่งเน้นงานที่มีคุณค่ามากขึ้น
4. คุณภาพสินค้าและบริการที่ดีขึ้น (Enhanced Quality)
- ระบบอัตโนมัติมีความแม่นยำในการทำงาน ลดข้อผิดพลาดจากแรงงานคน ทำให้สินค้ามีคุณภาพสม่ำเสมอและลดปัญหาของสินค้าด้อยคุณภาพ
- ระบบสามารถตรวจสอบและควบคุมคุณภาพได้แบบเรียลไทม์ ทำให้สามารถระบุปัญหาได้ตั้งแต่เนิ่น ๆ
5. ความยืดหยุ่นในการผลิต (Flexibility)
- Lean Automation ช่วยให้โรงงานสามารถปรับการผลิตตามความต้องการของลูกค้าได้อย่างรวดเร็ว เช่น ปรับปริมาณการผลิตหรือลักษณะผลิตภัณฑ์ตามความต้องการ
- ทำให้โรงงานสามารถตอบสนองต่อความเปลี่ยนแปลงของตลาดได้อย่างมีประสิทธิภาพ โดยไม่ต้องหยุดการผลิต
6. เพิ่มขีดความสามารถในการแข่งขัน (Competitive Advantage)
- Lean Automation ช่วยให้โรงงานผลิตสินค้าได้รวดเร็วและคุ้มค่ามากขึ้น สามารถส่งสินค้าได้ตรงเวลาและมีคุณภาพสูง ส่งผลให้มีความสามารถในการแข่งขันที่สูงขึ้นในตลาด
- ความยืดหยุ่นและประสิทธิภาพของ Lean Automation ช่วยให้บริษัทสามารถปรับตัวและนำเสนอสินค้าได้รวดเร็วมากขึ้น เพิ่มโอกาสในการครองส่วนแบ่งตลาด
7. พัฒนาคุณภาพชีวิตของพนักงาน (Improved Workforce Utilization)
- Lean Automation ช่วยให้พนักงานได้โฟกัสงานที่ซับซ้อนและมีคุณค่ามากขึ้น แทนการทำงานที่ซ้ำซ้อน ทำให้พนักงานมีทักษะและความรู้เพิ่มขึ้น
- ลดความเหนื่อยล้าและความเสี่ยงจากงานที่อันตรายหรือมีความซ้ำซ้อนสูง ทำให้สภาพแวดล้อมในการทำงานปลอดภัยขึ้น
8. ข้อมูลที่มีประโยชน์ต่อการตัดสินใจ (Data-driven Insights)
- Lean Automation เชื่อมต่อกับระบบ IoT และเซ็นเซอร์ต่าง ๆ ทำให้สามารถเก็บข้อมูลการผลิตและการดำเนินงานได้อย่างละเอียด
- ช่วยให้ผู้บริหารสามารถใช้ข้อมูลเพื่อวิเคราะห์และตัดสินใจได้อย่างแม่นยำ เพิ่มประสิทธิภาพในการวางแผนและปรับปรุงกระบวนการอย่างต่อเนื่อง
Lean Automation ไม่ได้เน้นที่การใช้เทคโนโลยีอัตโนมัติในทุกจุดเท่านั้น แต่ยังมุ่งพัฒนาทั้งกระบวนการให้มีคุณค่า ลดของเสีย และเพิ่มประสิทธิภาพโดยรวม ทำให้สามารถตอบสนองต่อความต้องการของตลาดและลูกค้าได้ดีขึ้น
การลงทุนในระบบอัตโนมัติมีต้นทุนสูง จึงควรศึกษาข้อมูลอย่างละเอียดเพื่อให้มั่นใจว่าคุ้มค่า แม้ว่าจะมีอุปกรณ์หลากหลายและเทคโนโลยีล้ำสมัยในท้องตลาดที่สามารถติดตั้งเพิ่มเติมได้ แต่การใช้แนวคิด Lean Automation จะช่วยให้คุณสามารถออกแบบระบบได้อย่างรอบคอบ ลดค่าใช้จ่าย (Low-cost Automation) พร้อมเพิ่มประสิทธิภาพการผลิต (High Productivity) ให้กับไลน์การผลิตของคุณได้อย่างยั่งยืน