LEAN Automation: Eliminating the 7 Wastes in Production Systems
The integration of automation in factories to boost productivity and reduce costs is both a key goal and a challenge for factory managers, especially those aiming to develop a Smart Factory to meet the growing market demands. However, transforming a factory into a smart one isn’t just about investing in expensive machinery or advanced robots. More importantly, it involves preparing the workflow before integrating it with automation systems, and LEAN Automation is the key. Today, Solwer will explain what LEAN Automation is and how it benefits industries in the 4.0 era.
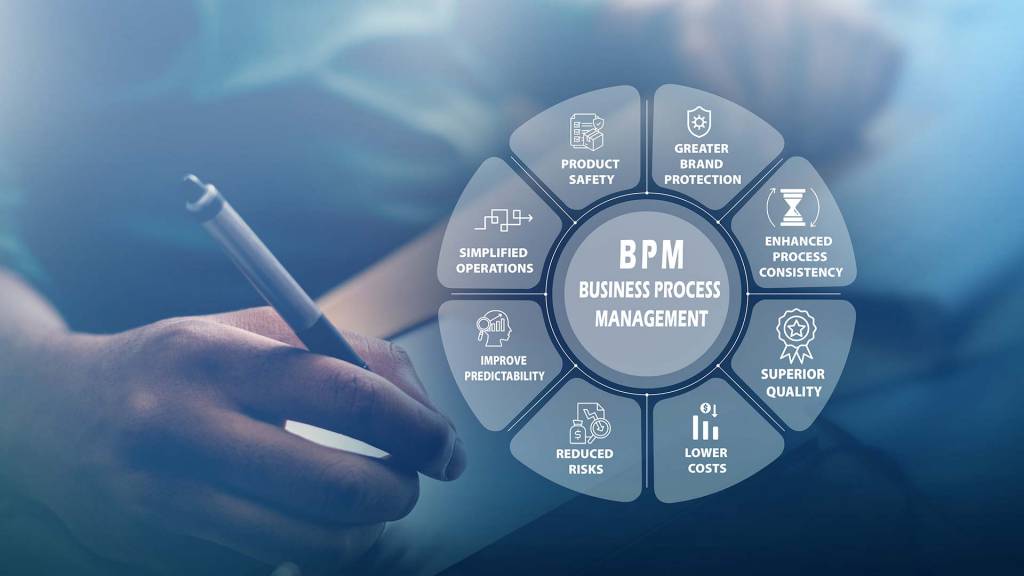
What is Lean Automation?
You May Also Like
LEAN Automation combines lean principles with automation systems, focusing on improving production processes to add value for customers. It’s not just about increasing the efficiency of each step, but also considering the benefits customers get from the product while striving to minimize costs.
When people think about automation, they may assume it will increase expenses, conflicting with lean principles aimed at reducing costs. However, the cost reductions in lean are not only financial but also about designing the most cost-effective and efficient processes, without always needing expensive equipment.
Principles of Lean Automation
2. Waste Reduction
Uses automation technology to reduce various wastes, such as errors, waiting times, and unnecessary movements, through systematically designed processes.3. Right-Sizing Investment
There’s no need to heavily invest in automation for every process. Invest only in areas that truly add value and reduce waste.4. Flexibility & Responsiveness
Design automation systems to be flexible, adapting to changes in market demands and customer needs without halting production.Differences Between Traditional Automation and Lean Automation
1. Implementation Goals
Traditional Automation: Focuses on increasing production capacity by automating repetitive tasks, replacing human labor to reduce errors and increase speed, but does not address unnecessary steps. LEAN Automation: Focuses on reducing waste and creating value for customers, improving processes for optimal results, and using automation technology only when necessary to enhance efficiency.2. Cost Reduction Methods
Traditional Automation: Reduces long-term costs by replacing human labor with machines to produce more in the same or shorter time, though initial investment may be high. LEAN Automation: Reduces costs at every step by improving processes to be more efficient, using resources effectively, and investing only where necessary, without always needing costly new technologies.3. Production Flexibility
Traditional Automation: Typically designed for repetitive tasks or mass production, offering limited flexibility for change. LEAN Automation: More flexible, as it is designed to adapt to specific, diverse production needs and market changes without halting production.4. Focus on Process Improvement
Traditional Automation: Emphasizes increasing output and reducing costs by replacing human labor without focusing on eliminating non-value-added steps. LEAN Automation: Focuses on continuous process improvement, eliminating unnecessary steps, and increasing efficiency by automating only the necessary tasks.5. Technology Investment
Traditional Automation: Often involves significant investment in machines or systems for repetitive tasks. LEAN Automation: Invests in technology that aligns with processes that need actual improvement, ensuring cost-effective usage of technology.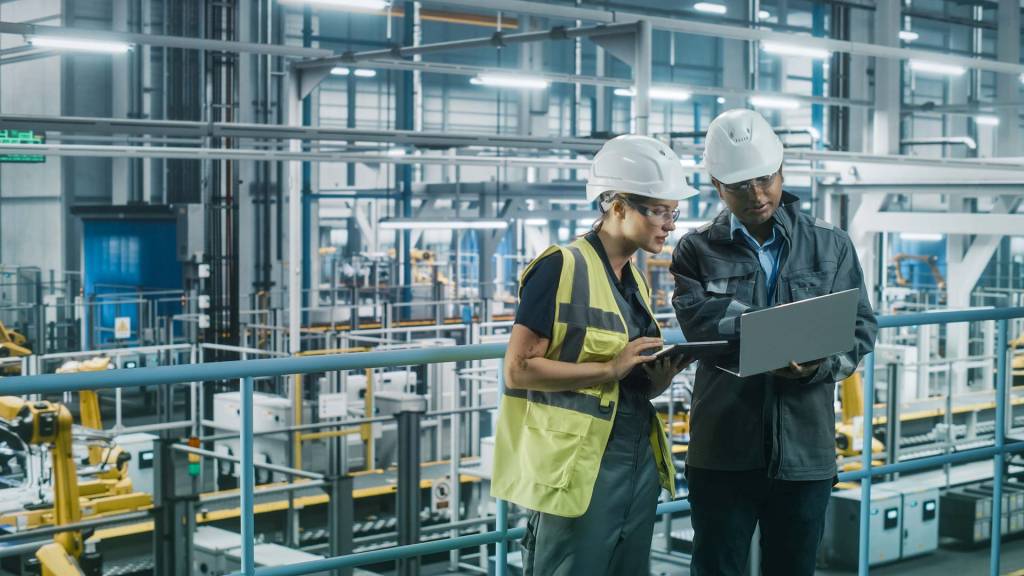
Effective Lean Automation Design by Denso
Denso places great importance on preparation and system design as the foundation for effective automation. Lean Automation design isn’t just about replacing people with robots; it also incorporates human skills in designing automation systems. The first step is to eliminate “Muda,” or waste, in the workflow. Using the Lean Manufacturing concept, it identifies 7 key wastes: Overproduction, Inventory, Transportation, Motion, Processing, Delay, and Defects. These wastes should be eliminated to ensure streamlined, efficient, and continuous processes. Following Lean Automation principles, system design focuses on reducing waste while enhancing productivity. As Sato Kenshu states, “The best production process is one that is simple and continuous.” Understanding Lean Automation principles helps organizations design and improve systems that quickly respond to market demands, reduce costs, and create a competitive advantage.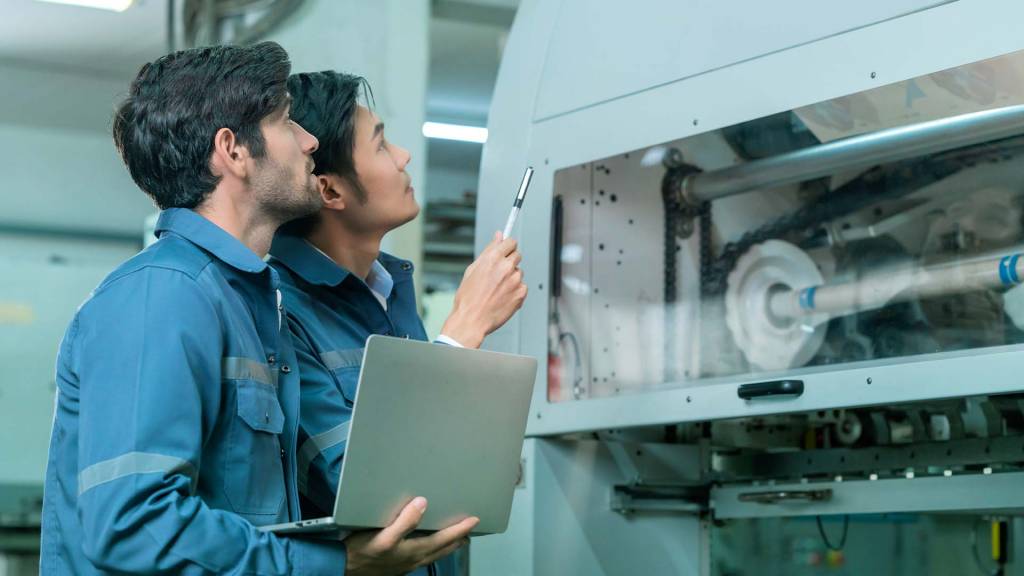
Steps to Implement Lean Automation in Factories
1. Process Analysis
Study the entire production process to identify current issues, such as waste in various steps, or inefficient use of time or resources. Create process maps to identify non-value-adding or problematic steps, including areas where automation could improve.2. Define Lean Objectives
Set clear goals, such as reducing production time, lowering costs, minimizing human error, or improving product quality. Identify KPIs (Key Performance Indicators) to track the results of Lean Automation implementation.3. Process Redesign
Simplify and make processes more efficient by eliminating unnecessary steps and combining processes that can be done together to reduce time and resource wastage. Consider automating repetitive tasks or those requiring high precision, such as assembly, packaging, or quality inspection.4. Select Appropriate Automation Technology
Choose automation technologies that meet the needs, such as robotic arms, sensor-based inspection systems, data analysis software, or IoT systems to connect production data and processes. Focus on selecting cost-effective technologies that provide value, without necessarily opting for high-end, expensive solutions unless they meet the specific cost-reduction needs.5. Pilot Testing
Test the Lean Automation system in a specific area of the factory to evaluate its suitability for real-world use. Check whether the system reduces waste, improves accuracy, and meets the set process improvement goals, adjusting for any issues that arise during the test phase.6. Employee Training
Train employees to understand how to operate Lean Automation systems and maintain equipment, ensuring they can use the system effectively. Create an understanding of Lean principles so all employees focus on waste reduction and adding value in production processes.7. Full-scale Implementation
Implement Lean Automation across the entire production process according to the plan tested. Install sensors and tracking systems to collect operational data, helping management monitor results and continuously improve operations.8. Monitoring and Continuous Improvement
Monitor the performance of Lean Automation using collected data, such as production time, waste reduction, and work efficiency. Continuously improve processes based on KPI evaluation, seeking ways to reduce further waste.
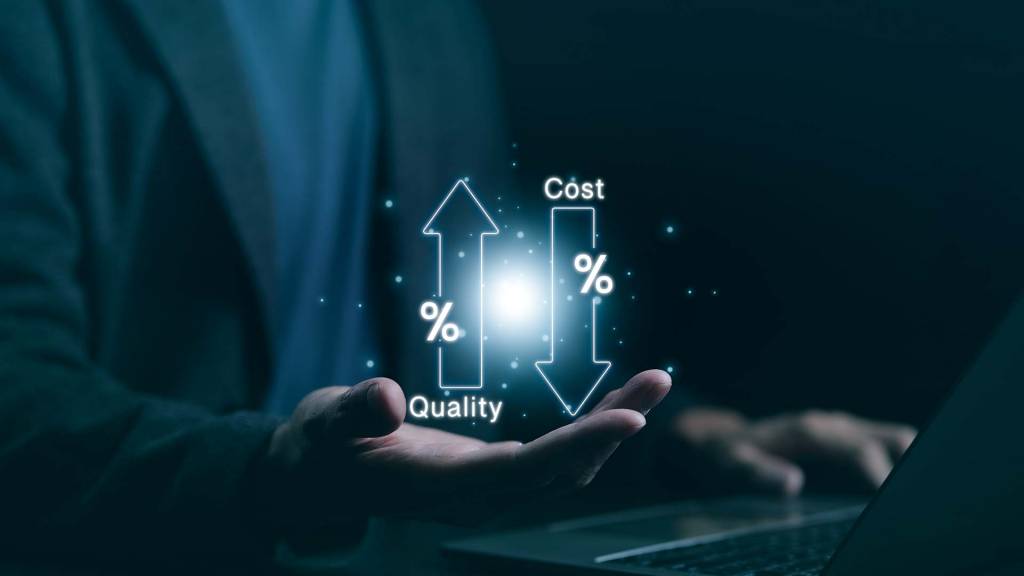